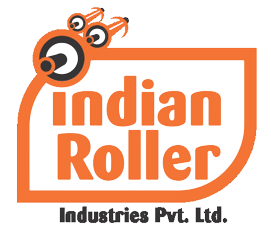
Plot No. 62/2/1, Sahibabad, Ghaziabad, UP India
Our group of specialists is taken part in assembling a scope of Rexine rollers. These rollers are planned according to the latest things winning in the business and fabricated utilizing the high-grade unrefined substance. The scope of Rexine rollers that we deal with can be modified on different boundaries like aspects and the material utilized for the manufacturing cycle.
Contact rollers are commonly used in manufacturing processes such as printing, laminating, and paper processing, where they provide pressure and support for the material being worked on. They can also be found in conveyors, where they help move materials along a production line.
Get a QuoteEmbossing rollers can be customized to meet specific requirements, and the pattern can be changed or updated as needed. They are often used in combination with other printing techniques, such as foil stamping or letterpress, to create a unique and high-quality finished product.
Benefits – Cover couch seat rollers for erosion and wear-obstruction.
Get a Quote
Printing rollers are commonly used in the Rexene industry to transfer ink, adhesive, or other coating materials onto the surface of the synthetic leather substrate. These rollers are typically made of a hard, durable material and are precision-engineered to ensure a consistent and high-quality print or coating application. Printing rollers are used in various processes within the Rexene industry, including embossing, printing, and coating.
Get a QuoteCoating rollers are widely used in the rexene (artificial leather) industry for applying coatings and finishes to rexene materials. Rexene is a synthetic material made of PVC or PU (polyurethane) and is commonly used as an alternative to leather in various applications such as upholstery, clothing, footwear, and accessories.
Get a QuoteLamination rollers are commonly used in the rexene (synthetic leather) industry for the lamination of two or more layers of rexene. These rollers are made of high-quality materials such as steel, rubber, and polymer, which allow them to withstand the high temperatures and pressures involved in the lamination process.
Get a Quote